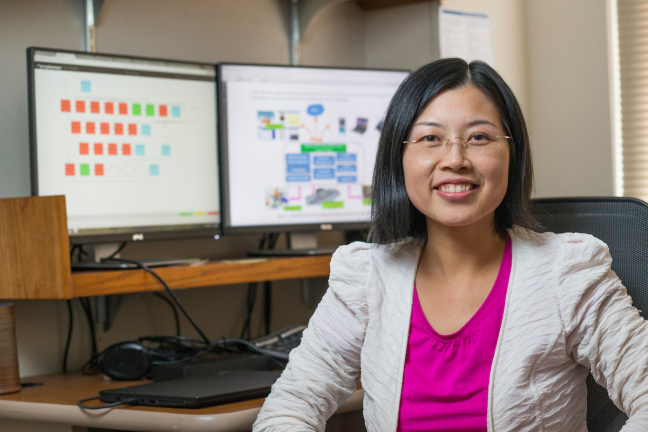
This article was originally featured on Iowa State University News Services by Mike Krapfl. Click here to read the original article.
AMES, Iowa – Reports of missing parts, machinery problems or any other issues on a factory floor don’t always move quickly to decision-makers.
Sometimes, data collection is workers writing a few notes on a pad. It could be hours or sometimes even days before managers see the notes and make corrections.
That can cause delays, increase costs and frustrate customers.
Guiping Hu, an associate professor of industrial and manufacturing systems engineering at Iowa State University, is working with several companies to develop a data-driven, real-time solution.
She calls it FactBoard. It’s a software system that’s designed to take in all the information that’s available on a factory floor and display it on visual dashboards so it’s accessible and useful.
“Companies collect data from the shop floor – a rich amount of data,” Hu said. “It’s collected, but it’s not often utilized in a timely, effective and efficient manner.”
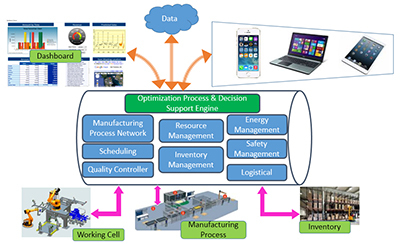
So Hu, who has studied supply chain and manufacturing systems optimization from her graduate school days a decade ago at the University of Pittsburgh, is developing FactBoard with collaboration from manufacturers Deere & Co. and Boeing Co. She’s also working with Ames-based Proplanner, a company that provides manufacturing software and information technology support; and Factory Right, an Atlanta company that provides information technology to manufacturers.
Hu’s FactBoard research team includes faculty collaborators Sarah Ryan, Iowa State’s Joseph Walkup Professor in Industrial and Manufacturing Systems Engineering, who studies ways to support and improve decision-making; Lizhi Wang, an Iowa State associate professor of industrial and manufacturing systems engineering who studies mathematical modeling; and Caroline Krejci, a former Iowa State faculty member who studies simulations and is now an assistant professor of industrial engineering at the University of Texas at Arlington.
The two-year, $2.6 million project is supported by the Digital Manufacturing and Design Innovation Institute based in Chicago, with cost-share funds from Iowa State and the researchers’ industry partners.
While the study will result in conference presentations and papers for academic journals, Hu said the primary goal is applied research that results in software that makes measurable differences on factory floors.
Boeing and John Deere are planning to implement the software on their shop floors, she said. The software will be integrated into the factory’s existing computers, workstations and other hardware. It can also be called up on smartphones and other devices.
“FactBoard will import all of these data feeds from the shop floor into a central depository,” she said. “And then it will broadcast the information to the right people and assist the decision- making on the shop floor in a real-time, efficient and effective manner.”
A worker, for example, might notice a shortage of parts that could eventually halt production.
“The worker can put a logistics request/report into FactBoard,” Hu said. “FactBoard will send a message to the materials coordinator and the shop floor manager. The idea is to keep communicating – to get the right information to the right people at the right time.”
Depending on the urgency of the situation, FactBoard could send out batch emails, or a text message or a phone call, she said.
FactBoard will also analyze any production issues and help managers find solutions and make decisions, Hu said. In the case of that parts shortage noticed by a worker, FactBoard could help supervisors temporarily modify the production sequence.
To make sure FactBoard provides the information manufacturers need, Hu has sent graduate students to factory floors to collect data, identify problems, write specifications and study interfaces with existing hardware. Building FactBoard on an existing software platform developed by Proplanner has allowed the research group to develop deployable software within one year and begin testing on factory floors.
Hu said the initial testing will include fixing bugs, changing specifications and collecting manufacturer feedback – all with big goals in mind.
“Manufacturers expect FactBoard to help them continue smooth operations, reduce delays, reduce inventory and improve customer happiness,” Hu said. “They want to see production that’s more efficient and effective.”