Alexander Goldman: Stretching for new, better metal
Author: Lani McKinney
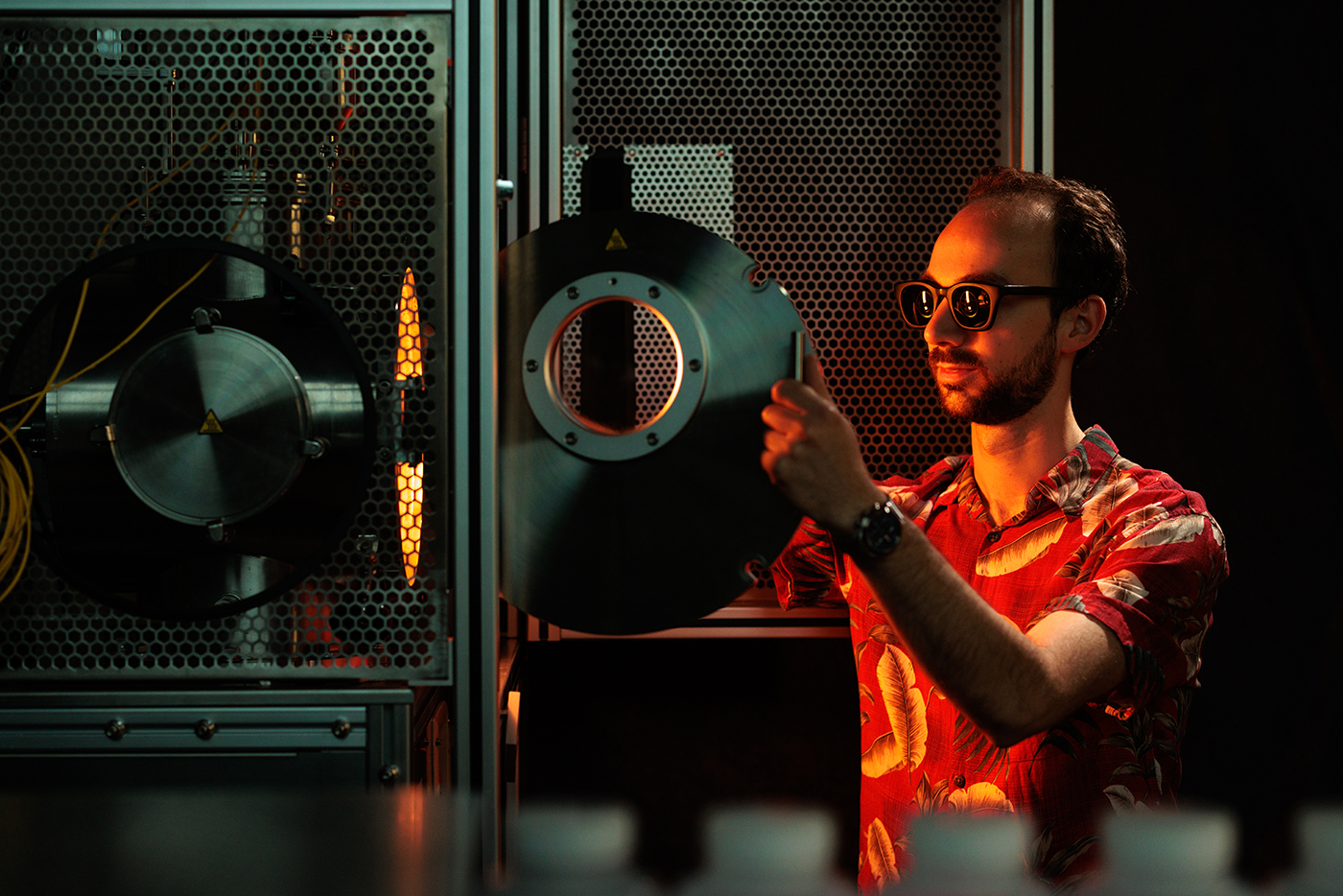
Author: Lani McKinney
When industrial engineering associate professor Bin Li made his move from University of Nevada, Reno, to Iowa State University two years ago, industrial engineering graduate student Alexander Goldman (who was a student of Li’s in Reno at the time) was glad to follow.
“Being mentored as an undergraduate student by Dr. Li taught me the wisdom of being patient. I love learning, and Dr. Li’s enthusiasm keeps me excited about research” says Alexander, “When Dr. Li decided to move to Iowa State University, there was no doubt I wanted to follow and pursue my PhD under his mentorship.”
Li’s research interests include the design and manufacturing of new lightweight alloys for automative and aerospace applications for improved fuel efficiency, computation-guided advanced manufacturing of new alloys and developing new advanced manufacturing approaches.
The goal in manufacturing is always to use the most viable metal, something affordable and light yet consistently safe. Many like to use aluminum because it’s a light metal and doesn’t break easily. However, Alexander hopes his research will yield a better metal alternative.
“Magnesium is even lighter than aluminum,” he says. The hurdle with magnesium, however, is it can be brittle. Alexander hopes by adding just the right elements to magnesium he can make a lighter and stronger, more malleable metal option for manufacturing.
So, what’s the ultimate end goal? “Making a metal increase in both strength and malleability is the holy grail,” he says. And while Alexander admits it might be difficult to achieve, it’s highly desirable and he’s anxious to take on the challenge.
Currently, Alexander is conducting his research in various facilities on campus. After looking at atoms in a computer simulation to predict the best metal formulas to use, he starts by casting the metals into a copper mold using quick heat in the Slater Lab’s vacuum induction furnace.
Next, Alexander tests ductility of the metal created using equipment borrowed from Iowa State materials engineering researchers, associate professors Sid Pathak and Qi An, and AGH University of Krakow materials science professor Robert Chulist. “We are fortunate to have great collaborative relationships with other engineering researchers on campus and across the globe,” he says.
Once which metal structures merit further investigation is determined, Alexander takes a closer look at those select metals with powerful electron microscopes at Ames National Lab. Examining the atomic structure of the metals allows comparison with how they match up with the initial computer simulations and sometimes leads to surprising new discoveries.
“Ames National Lab is doing some of the best materials engineering research,” says Alexander, “They are a strong benefit for anyone doing research related to materials.”
Campus resources have also played a big part of his positive experience at Iowa State. Alexander enjoys his judo instruction with top notch, renowned judo instructors through Iowa State’s student organization, Martial Arts Club, and has earned his yellow belt.
Additionally, he’s found Iowa State’s Graduate Career Services office to be helpful in exploring career options during and after graduate school. “They offer courses that help you figure out career options beyond school which is extremely beneficial,” says Alexander.
It’s only been a short while, but Alexander is excited with the early developments in his research efforts. Already he’s been able to produce a metal alloy where increasing the strength does not decrease the ductility.
“I remember during testing, watching the metal stretching and stretching, and looking at my watch and realizing it was going a long time without breaking, and thinking, ‘What did I do wrong?’,” says Alexander. As it turns out, he did something right.
For Alexander, those are the moments that make learning so gratifying.