Product ‘launch’: Rocket team makes entrepreneurship part of the plan
Author: aere_trosta
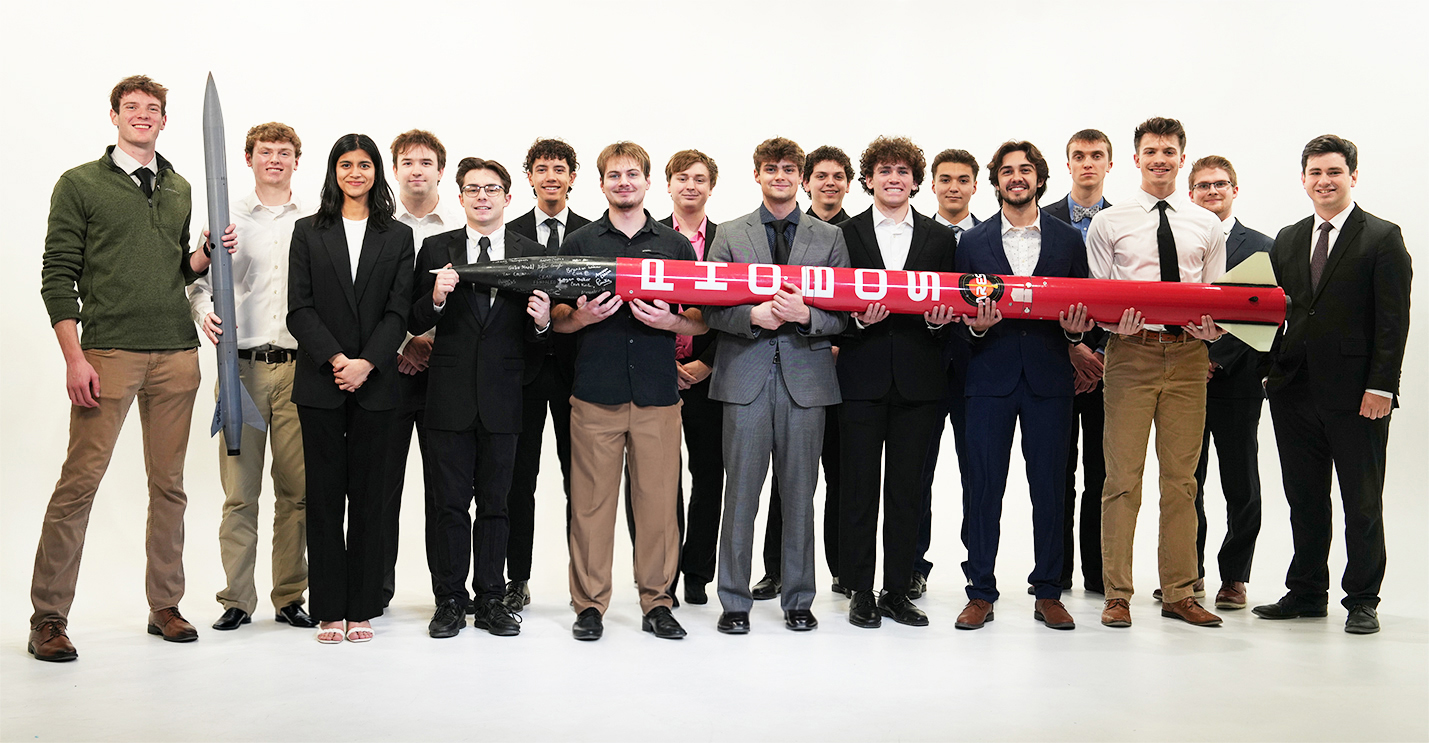
Author: aere_trosta
A group of rocket-building students in the Department of Aerospace Engineering has turned a class activity into a customer-focused business. In a unique twist to this type of student project, an entrepreneurial spirit is guiding the ARES rocketry team in the department’s Make To Innovate (M:2:I) program.
ARES, which stands for “Affordable Rocket Engineering Services,” is a “service-focused group that combines business aspects, engineering and everything in between,” says project manager Stephen Peterson.
The team is one of eight in the M:2:I program and is made up of 18 students in various engineering majors.
Instead of building rockets with the main goal of launch tests and competitions, ARES builds rockets to fulfill a wide set of customer requirements. They have developed multiple platforms with multiple missions and three teams to carry them out.
The vehicle team designs and builds rockets and organizes design processes. The operations team is responsible for launching rockets, gaining customers and making sure launches are happening reliably and effectively. The development team is responsible for maintenance and development of new capabilities on the rockets.
“It’s really a personalized experience,” mission manager Gabriel Hoehl says. “My job specifically is doing customer relations and the sales engineering aspects. I listen to customer needs and provide them with what they need.”
One current customer comes in the form of another aerospace engineering course, AERE 3610, which creates CLUE boards, microcontroller boards with many sensors. The ARES rocket payload bay was designed in-house specifically to accommodate those CLUE boards.
When it was discovered that the rocket’s original engine was too powerful for the CLUE boards to survive when launched, the development team re-engineered the platform to fly on a lower impulse motor which would provide a lower g-force launch. “By launching at a lower g-force, ARES is able to provide a more reliable and professional service to the 3610 course,” says Peterson.
Along with designing and building rockets, the team noticed a deficit in the area of testing cube satellites (CubeSats), which are small, standardized satellites used for space exploration, scientific research and more. They are popular among college curriculums as student projects. According to data shared by the team nearly 50% of cube satellites fail on launch. CubeSats are expensive, and ARES wants to improve that statistic to bring more CubeSats into the “mission success” category, so the team offers a six-axis vibration test for customers to get their rockets prepared and validated for launch.
There are three translational movements (forward/backward, up/down, left/right) and three rotational movements (pitch, yaw, roll), that are tested, says Peterson. If something like a wire is not properly secured or a sensor is not mounted correctly, the CubeSat can fail, so the testing offered by the team is valuable.
Currently, ARES has two main rockets they have constructed, named Phobos and Scylla. Phobos was constructed out of fiberglass in 2018 and is the bigger of the two. Its original mission was to test CubeSats for launch. Scylla is a fully 3D-printed rocket, built in 2022, which gives the team the advantage of handling quick manufacturing turnarounds. Because of its easily repairable 3D-printed parts, Scylla is a great tool for many customers and potential customers. The team hopes to launch Scylla in April, 2025.
ARES is currently working on construction of a new supersonic rocket made from carbon fiber material. It will be able to fly at an altitude of up to 15,000 feet and pull up to a 12g force — 12 times the measure of the gravitational force — which is a metric that spikes customer interest. By launching to a higher altitude, the team can give customers a longer flight time to test their products.
Hoehl spoke of the importance of the opportunities M:2:I provides: “Engineering skills require real-life application in order to perfect the craft. M:2:I creates the perfect opportunity. I like to think of this as a job. The professors really let you work your mind.”
The ARES project is supported by funding provided by Make to Innovate (M:2:I), the Department of Aerospace Engineering and the Iowa Space Grant Consortium (ISGC) at Iowa State University. Make to Innovate is sponsored by Boeing and Collins Aerospace. This project/material is based upon work supported by the Iowa Space Grant Consortium under NASA Award No. 80NSSC20M0107. This project also receives support from the ISU Pappajohn Center for Entrepreneurship and HartSmart Products.